Nautical Structures is proud to announce that the largest gangway it has built to date has been fully delivered, installed, commissioned, and handed over to the end user. This project is the culmination of 8 years of collaborative design with the shipyard, Edison Chouest Offshore: LA Ship Facility, the end user Viking River Cruises, and Nautical Structures industries. For us, it was truly a team effort from contract specification, design & engineering, fabrication, assembly, project management, and the NSI Service group.
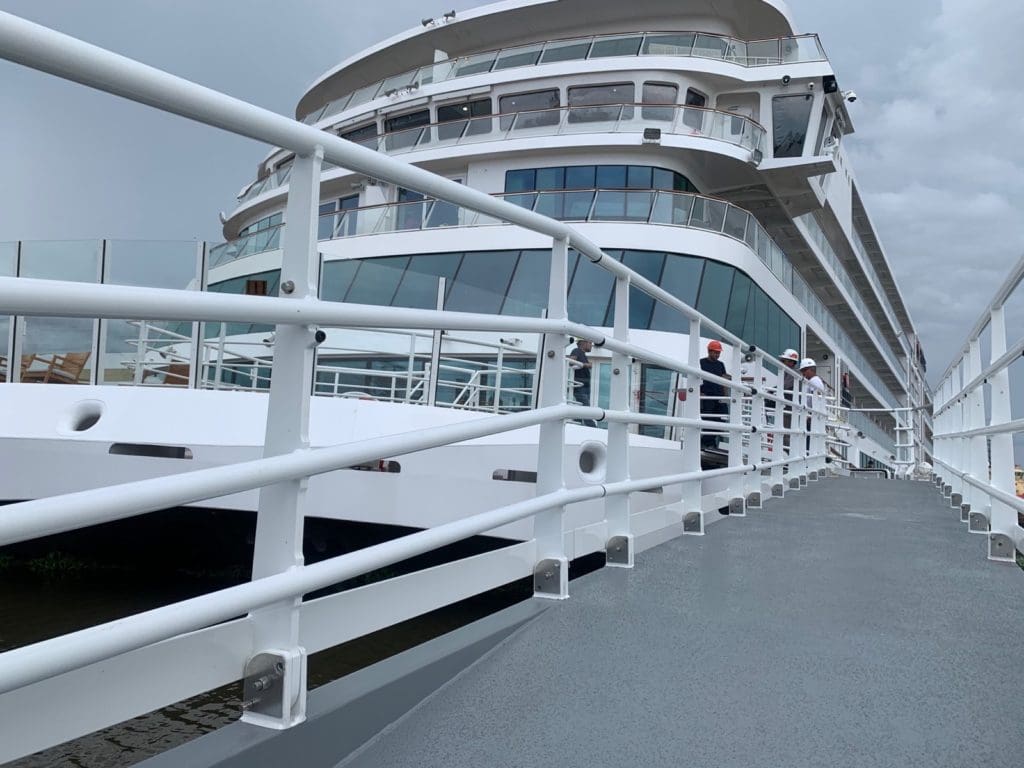
Starting with delivery and final assembly, the unit is so large (114’ end to end if completely open) that it had to be shipped in multiple pieces due to the weight and size. Once pre-assembly was conducted at Nautical Structures HQ and the pieces were on-site in Louisiana, the final assembly was begun in an empty bay at the shipyard. A special thank you to the Edison Chouest Offshore team for being accommodating to the NSI Service team and assisting in the installation and commissioning.
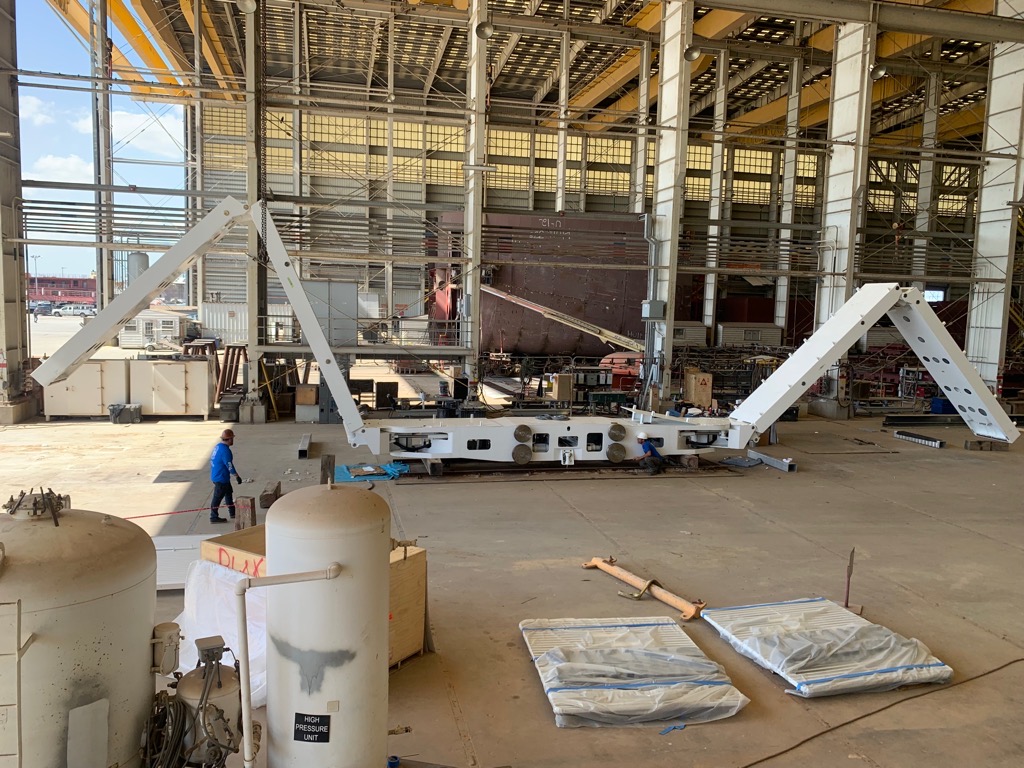
Once the gangway was fully assembled and tested, it was time to roll it into the boat and begin the commissioning process. The gangway is unique in that it services both sides of the vessel and travels to either Port or Starboard via train tracks & wheels. This created a necessity to have the unit completely self-contained when it comes to hydraulics, electrical controls, and other critical systems. After all of these connections were made to the ship, and the gangway started up and fully function tested it was time to conduct the Harbor Acceptance Test and ABS (American Bureau of Shipping) witnessed Load Testing.
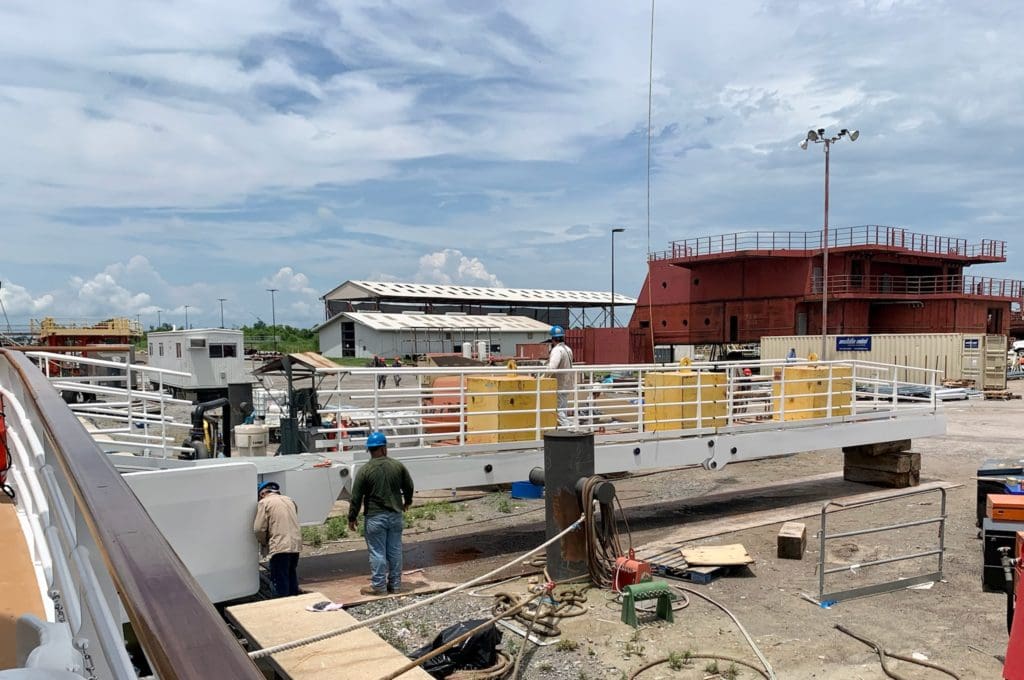
With a successful Harbor Acceptance Test completed it was time for end user handover and crew training. Our service team took the key players at the shipyard as well as the vessels engineering staff through the ins and outs of the system. They were briefed on basic operation and deployment/stowing procedures, how to arrange the adjustable hand-rail system, conducting troubleshooting and emergency operations, as well as basic maintenance to keep the unit looking like it belongs on a luxury cruise vessel.
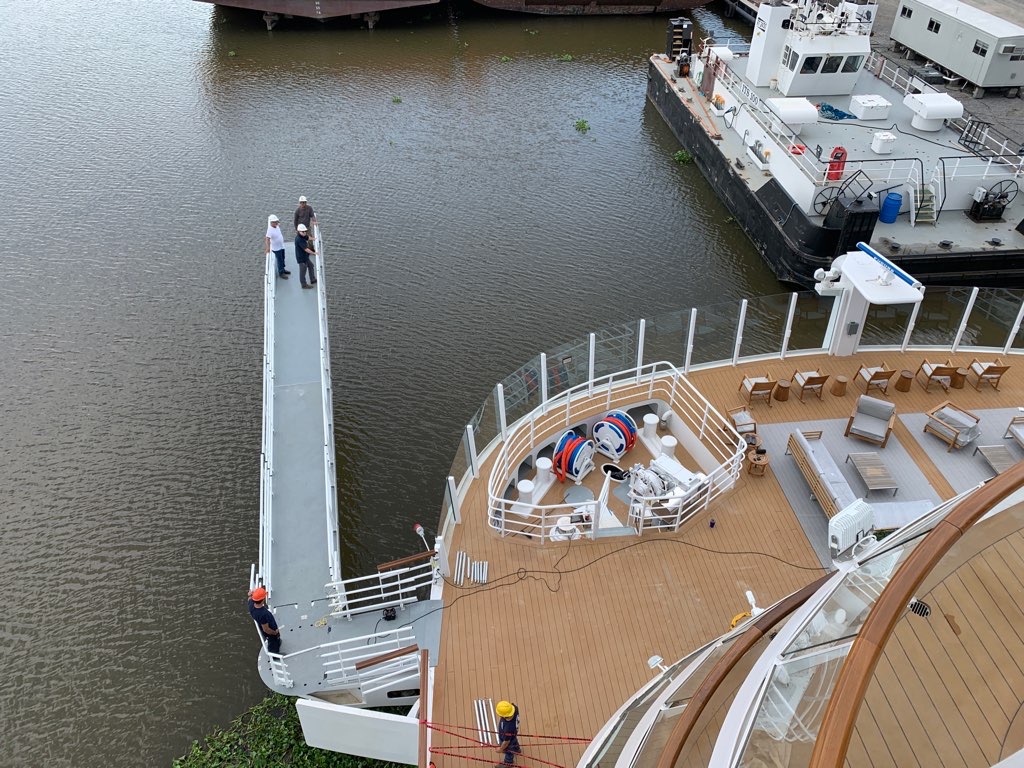
Again, Nautical Structures is so proud to be a part of such an ambitious Made in the USA project. Thanks to all parties involved in making this a reality: Edison Chouest Offshore, Viking River Cruises, American Bureau of Shipping, and most importantly the Nautical Structures staff who made it possible.
To learn more about how Nautical Structures can help with your next bespoke project please don’t hesitate to reach out via email here or visit our contact page here.